设备管理系统拆解
设备管理系统通过统一管理资产、优化资源配置提高资产利用率;通过预防性维护、备件管理、能耗管理降低运营成本;通过自动化管理、实时数据监控提升运营效率;通过安全检测、故障预测与预防增强安全性和可靠性;通过数据分析与反馈、技术驱动促进持续改进和创新。
这些价值共同作用于企业的生产经营活动,为企业创造更大的经济效益和社会效益。
01 设备管理
设备管理系统主要实现设备资产的管理,包含设备生命周期的管理,从规划设计、选型与采购、安装调试、验收入库、使用维护、改造更新、报废出库;包含设备使用过程管理,包含设备台账管理、点检、巡检、保养、润滑、盘点管理。
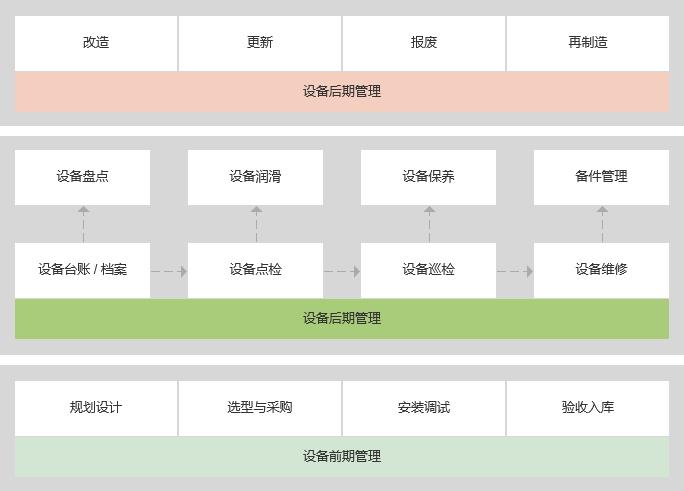
设备管理系统核心功能
设备点检管理遵循“八定”原则:
定点:明确设备的点检部位,这是设备点检的基础。通过对设备的结构和功能进行深入分析,确定哪些部位是关键点,需要定期进行点检。
定标准:为每个点检部位制定明确的检查标准。这些标准可以是定量的,如温度、压力、振动等参数的具体数值范围;也可以是定性的,如外观是否完好、有无异常声音等。
定人:明确点检工作的责任人。每个点检部位或区域都应指定专人负责,以确保点检工作的有效性和持续性。
定周期:根据设备的运行状况和点检部位的重要性,制定合理的点检周期。不同的设备和点检部位可能需要不同的点检频率,以确保及时发现潜在问题。
定方法:确定点检的具体方法和步骤。这包括使用何种工具、如何进行测量、如何记录数据等。通过科学的方法,可以提高点检的准确性和效率。
定量:在点检过程中,尽可能对关键参数进行量化测量。量化数据有助于更准确地评估设备的运行状况,并为后续的决策提供支持。
定业务流程:制定设备点检的业务流程,包括点检前的准备、点检过程中的操作规范、点检后的数据记录和处理等。通过规范的业务流程,可以确保点检工作的有序进行。
定点检要求:明确点检工作的具体要求和目标。这包括点检的精度、数据的准确性、问题的及时报告和处理等。通过明确的要求,可以提高点检工作的质量和效果。

设备管理主功能清单
设备润滑管理在减少磨损、提高设备效率、降低维护成本、保障生产安全、提升产品质量、减少能耗、增强环保意识和提升管理水平等方面具有重要作用。设备管理系统中特增设“设备润滑管理”。
设备润滑管理遵循“五定”原则,定时、定点、定质、定量和定人:
定时:根据设备结构特点、工作环境及润滑油品的消耗情况,确定两次加油间隙时间。确保设备在需要时得到及时润滑,避免因润滑不足而导致的磨损加剧。
定点:根据设备各部位运行特点,确认需要润滑的部位,并作出统计,载入润滑管理手册,以利于操作人员逐点加油。确保设备所有需要润滑的部位都能得到有效的润滑,防止遗漏。
定质:根据轴承类型、运行状态以及载荷特点,选用适合的润滑油品种。确保使用的润滑油能够满足设备的运行要求,避免因油品不合适而导致的设备故障。
定量:根据加油部位的容积和消耗情况,确定每次的加油量。既要保证设备得到足够的润滑,又要避免浪费和过量加油可能带来的问题(如增加运动阻力)。
定人:明确操作人员或维护人员对每台设备润滑工作应负有的责任。确保设备润滑工作得到落实,责任到人,便于管理和追溯。
02 简道云设备管理与巡检
简道云设备管理与巡检系统:实现设备的全生命周期一体化监管,规范化的设备巡检、保养管理流,发现和预防设备故障,多维经营数据统计分析支撑各环节管理决策,实现设备健康运行,保障生产安全和效率。
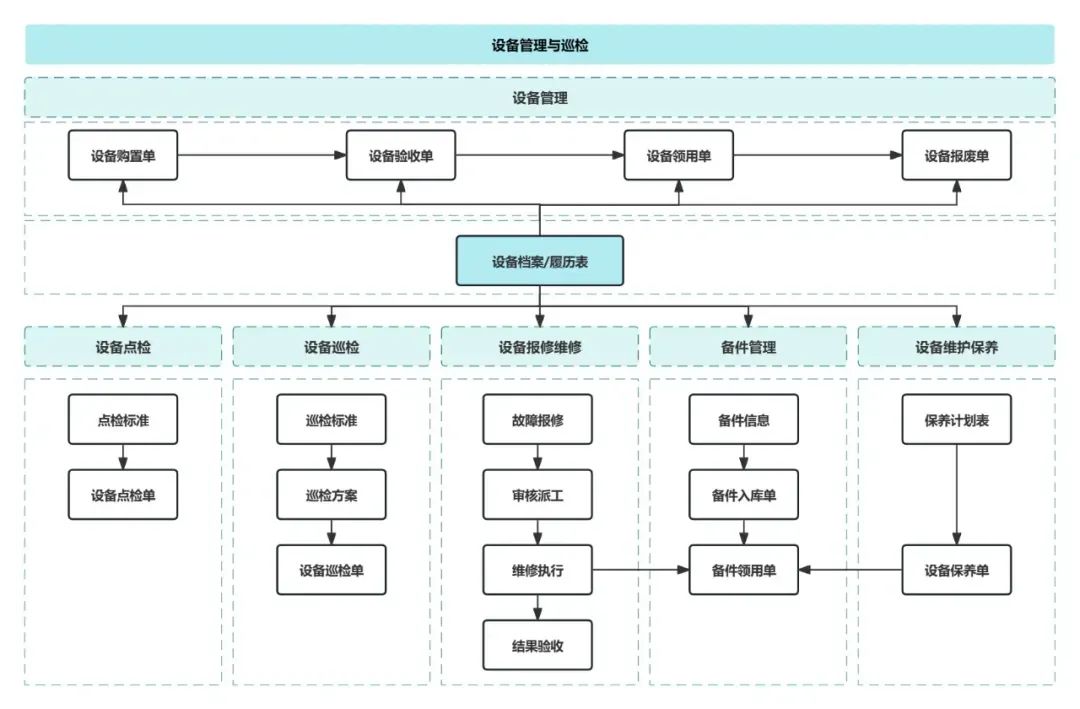
简道云设备管理与巡检系统业务流程图
简道云使用低代码模式,已完成设备管理与巡检的基础版本搭建,在主体业务和当前一致的情况下,可以部署使用。在具体页面和功能存在有少量差异,可以依据当前版本进行更新完善,其低代码方式将提供极大的兼容性。
若是核心流程存在较大差异,则可以以当前版本为蓝本,直接重新搭建。
简道云搭建方式为组件化搭建,展示页面变动则数据存储格式变动。较为麻烦一点的是,某一字段涉及多个页面,则需要挨个地方去处理,哪怕该字段在某些页面是默认值或可隐藏状态。
在全新一代低代码工具,也可以使用面向对象思维构建数据模型,通过调整模型来实现字段的增减,从而在必要的页面再更新即可。
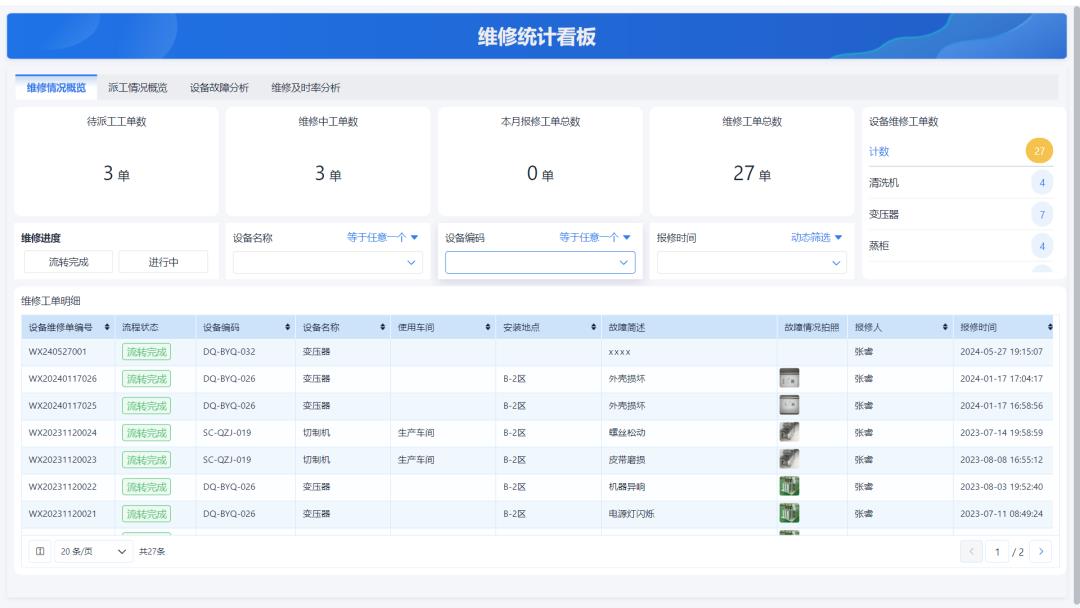
简道云维修统计看板
03 设备综合效率-OEE
OEE(Overall Equipment Effectiveness),即设备综合效率,OEE是一项指标,确定了真正有效的计划生产时间的百分比。
设备综合效率OEE = 时间开动率×性能开动率×合格品率 。
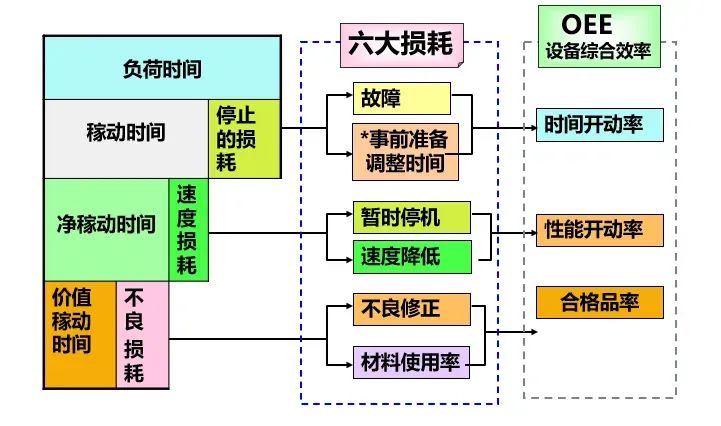
设备综合效率损耗
计算举例:
某工厂实施8小时作业体制,其中中午休息1小时(不含在作业体制内),上班时间包括早会,检查,清扫等20分钟,上、下午期间各休息15分钟。
有一台设备,因应市场需要,每天加班30分钟,该设备理论节拍为0.8分钟,在正常稼动时间内应生产575件,但实际仅生产出418件,实际测得的节拍为1.1分钟,当天更换刀具及故障停机时间为70分钟。
不良率维持2%。
请问该设备的设备综合效率为多少?
计算:
追究OEE的本质内涵,其实就是计算周期内用于加工的理论时间和负荷时间的百分比。
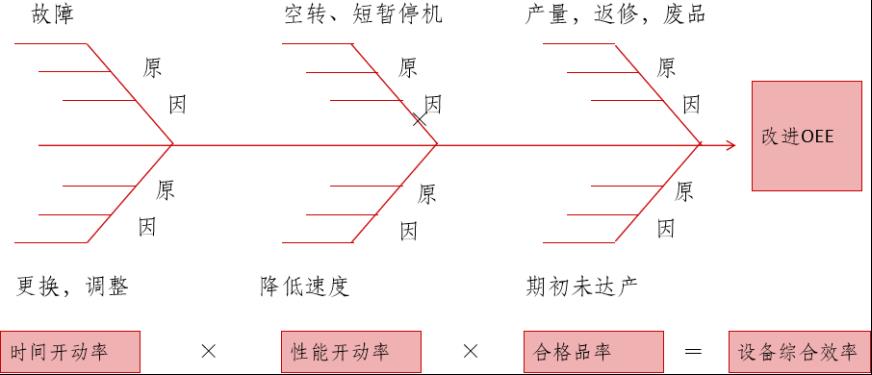
提升OEE方案
要提升OEE,就需要在具体影响因素上找原因,逐个去克服和优化。
持续完善是精益生产的一直追求。
设备管理系统还可以出具相关统计报表,跟进点检、巡检、润滑、维修的执行情况;接入IOT模块,还可以构建孪生模型,实现生产环境的数字模拟,为产线少人化、无人化奠定基础。