从 “停工待料” 到 “高效生产”,物料齐套性检查如何让混乱车间秒变高效“流水线”?
检查检查
在生产制造的生产现场,是否遭遇过这样的“噩梦”场景:
车间里,机器闲置轰鸣,生产进度却停滞不前,只因工人们还在焦急地等待物料;
仓库里,一边是空荡荡的产品架,另一边是堆积如山的半成品,只因缺几个关键零件而无法完工;
产线上,部装班组热火朝天,总装班组瞌睡闲散,只因总成框架物料物流意外,流水线不能正常流动。
这些令人头疼的问题,根源往往在于物料的齐套性失控。
物料齐套性检查,看似平凡的环节,实则掌控着生产制造的“生死命脉”,直接关系到企业的成本、效率与声誉。
一
物料齐套性检查
是什么?
物料齐套性检查是指在生产制造过程中,对所需物料的种类、数量、规格和质量进行全面核查,以确保所有物料能够满足生产需求的过程。通常在生产前进行,以避免因物料短缺或不符合要求而导致的生产延误和质量问题。
物料齐套性检查的物料涵盖范围广泛,包括原材料、采购零件、外协配件、包材、工装模具等生产必备要素。
在汽车整车装配厂,生产线上的每一辆汽车都有成千上万个零部件,物料齐套性检查人员需依据生产计划和 BOM(物料清单),逐一核对发动机、轮胎、座椅、电子元件等零部件的库存数量、质量状况,确保开工时不会因零部件缺失或质量问题而导致生产线停滞。
在服装制造企业,要赶制一批新款服装,布料、拉链、纽扣、缝线等物料必须按时按量就位,齐套性检查不仅要确认物料数量够不够,还要查看布料颜色是否有偏差、拉链拉动是否顺畅等细节,只有物料完美“配齐”,生产才能顺利推进,产品才能按时交付到客户手中。
二
物料齐套性检查
重要性
在现代生产线上,各环节紧密相连,如同精密咬合的齿轮,一旦物料缺件,生产线便会瞬间陷入停工待料的僵局。
以一家大型家电制造企业为例,在生产旺季赶制智能空调订单时,由于关键的压缩机供应商突发生产事故,未能按时交付,导致装配车间多条生产线停工数日。
停工期间,厂房租金、设备折旧、工人闲置工资等成本每天高达数十万元。之后为了追赶进度,不得不安排工人加班加点,又额外增加了加班费支出。
不仅如此,订单交付延迟,还引发部分客户投诉,甚至有客户取消订单,转向竞争对手,给企业带来了巨大的经济损失与声誉损害。
若企业能提前通过严谨的物料齐套性检查,及时察觉压缩机供应隐患,便可提前调整生产计划,如临时调配其他供应商资源、优化内部生产工序等,避免生产线的长时间停滞,确保生产连续性。
物料齐套确保了产线的连续作业,有助于缩短产品的生产周期,提升产品交付率。
客户下单后,满心期待产品能按时、高质量送达。
对于一家知名手机品牌而言,新品发布会后订单量暴增,倘若因物料不齐套(如:摄像头模组供应不足),致使手机组装进度受阻,交付延期,客户在长时间等待后热情消退,会对品牌好感度骤降。
即便后续补齐货物,差评与负面舆论也已在网络蔓延,影响潜在客户购买决策。
若是还存在物料质量不达标引发产品质量问题(如:手机屏幕因使用不合格物料出现闪屏现象),售后维修成本飙升,客户投诉增多,品牌形象更是遭受重创。
反之,扎实做好物料齐套性检查,确保物料按时、按质就位,产品如期交付,客户体验佳,口碑相传,能为企业赢得更多市场份额与忠实客户。
物料齐套性检查可以提前发现物料短缺或不匹配的问题,从而及时采取措施进行补充或调整,避免因物料问题导致生产停滞或延误,确保生产计划的顺利实施。
物料管理不当极易造成成本的“黑洞”。
一方面,物料库存积压,企业资金被大量占用。
以某服装制造企业为例,因对市场流行趋势预估失误,囤积过量面料,不仅仓储成本逐月攀升,资金周转困难,还面临面料过时贬值风险。
另一方面,物料缺货导致生产中断,紧急采购成本高昂。
以电子制造企业在生产旺季遭遇芯片缺货为例,为保订单,高价从现货市场抢购芯片,成本远超预算。
物料齐套性检查有助于合理安排物料采购和库存,避免因物料过剩或短缺而造成的资源浪费,降低企业的生产成本,提高经济效益。
三
物料齐套性检查
检查流程
1
计划阶段:精准规划,打好基础
在生产制造的前期筹备中,计划阶段是物料齐套性检查的“导航仪”,为整个生产流程指引方向。计划员需依据精准的生产计划与详细的 BOM(物料清单),精确拆解出物料需求。BOM 作为物料需求拆解的关键“蓝图”,其准确性至关重要,任何细微的物料层级、用量偏差,都可能在后续引发物料短缺或积压的连锁反应,因此企业需定期维护与更新 BOM,确保其与产品设计、工艺变更同步。
同时,结合市场趋势、历史数据和销售预测来合理安排物料采购计划。市场趋势方面,关注原材料价格波动、新技术引发的物料更替等因素;历史数据能反映过往同期物料的消耗速率、采购周期;销售预测则基于市场调研、客户订单意向,预估产品销量。
2
执行阶段:严格把控,步步为营
采购订单下达后,执行阶段成为物料齐套性保障的“主战场”。采购人员需实时追踪订单执行情况,与供应商保持密切沟通,每日跟进物料生产进度、发货安排,掌握货物在途动态。一旦供应商反馈生产延误,如因原材料供应不足或设备故障,采购人员要迅速评估影响,协调供应商加急处理,或寻找替代资源。
货物到库后,仓库人员按照严格标准验收。验收内容涵盖物料数量、规格、质量等多维度,核对送货单与采购订单数量是否一致,用卡尺、量具等量具检测零部件尺寸精度是否达标,对原材料抽样进行性能测试。对于不合格品,立即贴上标识隔离,按流程启动退货、换货或特采(特殊情况下经评估让步接收)处理。
仓库还需定期盘点库存,采用实地盘点与系统对账结合,确保账实相符,库存准确率直接影响生产决策,精准的库存数据能让计划员放心安排生产任务,避免盲目开工后才发现物料账上有、库里无的尴尬局面。
3
检查阶段:细致核对,查漏补缺
在临近生产节点,检查阶段如同“安检关卡”,严格把关物料齐套状态。按照生产工单,物料专员要细致对比库存物料、在途物料与生产需求。检查频率依生产特性而定,对于订单生产型企业,工单下达后、开工前至少进行两次全面检查;对于批量连续生产企业,按生产批次定期检查,如每日开工前抽检重点物料,每周进行一次全物料覆盖检查,关键节点如新品试产、旺季生产前更要强化核查。
一旦发现缺料或齐套问题,立即详细记录并反馈。企业通常会组建跨部门小组协同解决,成员涵盖计划、采购、仓库、生产等部门。
常见问题如物料数量不足、质量瑕疵、供应商延迟交货等,解决策略各有侧重。
数量不足时,采购紧急补货,生产部门同步调整工序,优先生产物料齐全的半成品;质量问题,质量部门牵头判定影响,轻微缺陷经工艺调整可修复的安排返工,严重质量问题则追溯供应商换货;供应商延迟,采购施压催促,同时内部深挖库存潜力,调整生产计划优先消耗库存物料,通过灵活应变,确保物料尽快补齐、生产重回正轨。
四
物料齐套性检查
实用技巧与建议
1
加强供应商管理
供应商作为物料供应的源头,其优劣直接关乎物料齐套性。
在选择供应商时,不能仅看价格,而要全方位考量资质、信誉、供货能力等要素。与优质供应商建立长期战略合作伙伴关系,双方深度互信,共享市场趋势、技术革新等信息。
如汽车制造商与关键零部件供应商协同研发新产品,提前布局未来数年物料供应规划。
同时,定期对供应商绩效评估,从交货准时率、物料质量合格率、应急响应速度等维度量化考核,对表现不佳供应商辅导改进或及时汰换,确保物料供应“源头活水”源源不断,为物料齐套筑牢根基。
2
提升员工意识与能力
物料齐套性保障离不开每一位员工的精准操作。企业应定期组织物料管理培训,涵盖物料识别、仓储知识、质量检验、系统操作等内容。
在仓库管理培训中,教导员工依据物料特性分类存放,易燃品隔离、防潮品密封,运用 5S 现场管理法保持仓库整洁有序;物料检验培训传授抽样技巧、量具使用,让员工练就“火眼金睛”识别次品。制定清晰详细的物料操作规范手册,员工日常操作有章可循,减少人为失误。
鼓励员工反馈物料管理中的问题,设立奖励机制,对提出有效改进建议者给予表彰与物质奖励。
生产线上员工发现物料配送路线迂回导致延误,建议优化配送路径,经采纳后不仅提升物料齐套效率,员工也获得成就感,营造全员参与、持续优化的良好氛围,让物料齐套性在日常点滴中稳步提升。
3
持续优化流程
生产制造在动态发展,物料齐套性检查流程也需与时俱进。依据生产工艺变更、产品升级、市场需求波动等因素,定期审视流程。
比如企业引入新生产线,生产节拍加快,原物料配送频次与检查节点需相应调整;产品功能拓展新增零部件,BOM 及物料需求计划流程即时更新。
积极引入新技术优化流程,利用物联网实现物料实时追踪,从供应商仓库到生产线全程可视;大数据分析挖掘物料消耗规律、供应商交货周期波动,辅助精准决策。跨部门协作时,依据企业战略、业务重点灵活调整部门职责分工,打破“部门墙”,避免推诿扯皮,确保物料齐套流程顺畅高效,为企业生产运营注入源源不断动力,驱动企业在市场浪潮中稳健前行。
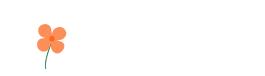
物料齐套性检查是生产制造中不可或缺的一环,对于保障生产进度、提高产品质量和降低生产成本具有重要意义。
物料齐套性检查贯穿生产全程,从物料筹备的源头,到产品交付的终点,每一个精准核查的瞬间,都为生产连续性保驾护航,为客户满意度添砖加瓦,为成本控制精打细算。
在数字化浪潮奔涌的当下,ERP、MES、工业大模型等前沿技术赋能,让物料齐套管理如虎添翼,企业得以拨开复杂生产的“迷雾”,精准掌控物料动态。
望各企业能深刻洞察其价值,夯实物料管理根基,持续优化流程、精进技术、提升团队,以物料齐套的“确定性”,从容应对市场的“风云变幻”,迈向高质量发展的康庄大道。