搬开绊脚石,解决精益生产八大浪费
在生产制造领域,【浪费】有着独特且明确的定义,是指不增加产品价值,却消耗了人力、物力、时间、场地等资源的活动。比如:工人花费额外的时间去搬运那些并非急需的原材料,搬运本身没有让产品变得更有价值,却消耗了工人的时间和体力,还可能占用运输设备等资源,这就是一种浪费。又或者,企业生产了大量超出市场需求的产品,这些多余的产品积压在仓库里,占用了库存空间,浪费了资金,却没有为企业带来额外的收益,这同样属于浪费行为。
八大浪费,是对生产制造过程中常见浪费类型的高度概括和总结,包括搬运、库存、动作、等待、过量生产、过度加工、缺陷(不良品)、未充分利用员工技能浪费,如同隐藏在生产环节中的 【暗礁】,阻碍着企业高效、低成本地运营,对企业的成本、效率、竞争力产生着深远的影响。
一
追根溯源
八大浪费的形成脉络
八大浪费的概念最早源于丰田生产系统(TPS) ,由丰田汽车公司的首席工程师大野耐一提出。
在早期,大野耐一总结出了七大浪费,包括搬运(不必要的产品、材料或人员移动)、库存(任何形式的未使用材料,包括原材料、在制品和成品)、动作(人员或设备的无效移动)、等待(由于流程不流畅或资源分配不当而导致的等待时间)、过量生产(生产超过需求的产品或服务)、过度加工(进行超过客户需求的加工步骤)和缺陷(不良品)(不符合质量标准的产品或服务,需要返工或报废),这些浪费通常用缩写 “TIMWOOD” 来记忆。
随着时间的推移和生产管理理念的发展,20 世纪 90 年代,当丰田生产系统在西方得到广泛采用时,西方国家引入了第八种浪费 —— 未充分利用员工的才能或技能,从而形成了如今的八大浪费,此时用 “TIMWOODS” 来概括这八大浪费。
在企业生产实践中,员工的技能和才华若得不到充分发挥,会造成人力智力资源的浪费。
某电子制造企业招聘了一批具有高学历和专业技能的员工,他们在电子电路设计、软件开发等方面具备较强的能力。然而,企业在生产安排上,只是让这些员工从事简单的产品组装工作,完全没有发挥他们在技术研发和创新方面的优势。这就导致员工的工作积极性受挫,同时企业也失去了利用这些员工的专业技能进行产品升级和技术改进的机会,增加了企业的人力成本,却没有获得相应的效益提升,这就是典型的未充分利用员工才能的浪费。
从七大浪费到八大浪费的演变,是对生产制造过程中各种低效和浪费现象认识不断深化的过程,也反映了企业在追求精益生产、提高生产效率、降低成本过程中,对管理理念和方法的持续探索与完善,以适应不断变化的市场环境和企业发展需求。
二
内容详情
八大浪费的解剖图谱
搬运浪费 - Transportation:不必要的【旅行】
搬运浪费是指在生产过程中,物品的搬运、放置、堆积、移动、整列等操作没有为产品增加价值,却造成了资源的浪费。在大型汽车制造工厂,零部件从仓库搬运到生产线的过程中,如果搬运路线规划不合理,或者采用了不恰当的搬运工具和方式,就会导致搬运时间增加、搬运设备占用过多,还可能造成零部件在搬运过程中损坏。此外,搬运过程中需要占用一定的空间,如仓库的存储区域、搬运通道等,这些空间如果用于更有价值的生产活动,将能为企业创造更多的效益。
库存浪费 - Inventory:空间的【吞噬者】
库存浪费是指生产过程中停滞的物料(包括原材料、在制品、成品),在生产线中并不直接创造价值,却带来了诸多损失。
从表面上看,库存需要占用仓库空间,增加搬运、堆积、保管费用,企业需要投入资金建设仓库、购买货架等设备,还需要安排人员进行库存管理。从潜在损失来看,库存占用了大量的流动资金,降低了资金的周转率,企业需要承担额外的资金利息。市场需求的变化还可能导致库存积压,增加销售风险和物品劣化的风险。
例如:服装行业若库存过多,当季节更替或流行趋势改变时,这些库存服装可能会滞销,只能降价处理,造成经济损失。
并且,大量库存还会掩盖生产过程中的问题,如设备故障、生产计划不合理等,使企业难以发现并解决这些潜在问题。
▲ 高库存会掩盖很多问题
动作浪费 - Motion:效率的【绊脚石】
动作浪费在生产线上较为常见,是指人和设备的动作对产品生产没有产生附加价值,却消耗了体力和时间。
以电子产品组装车间为例,工人在组装手机时,若物料摆放不合理,导致工人需要频繁地转身、弯腰去拿取零件,或者在操作过程中出现左右手交换、动作幅度过大等情况,都是动作浪费。
这些无效动作不仅降低了工人的工作效率,还会使工人更容易疲劳,增加工伤的风险,同时也会影响整个生产线的流畅性。
等待浪费 - Waiting:时间的黑洞
等待浪费是由于生产原料供应中断、作业不平衡、生产计划安排不当等原因,导致工人或设备在工序、作业、流程之间出现时间闲置的情况。
在汽车零部件生产线上,若上游工序的设备突然发生故障,导致零部件供应中断,下游工序的工人和设备就只能处于等待状态,造成人员和设备的闲置,浪费了生产时间。
生产线上不同品种之间的切换,如果准备工作不够充分,如模具更换时间过长、物料准备不及时等,也会造成等待的浪费。每天的工作量变动幅度过大,有时工人和设备忙不过来,有时又无事可做,这同样会导致等待浪费,降低生产效率。
过量生产 - Overproduction:多余的【负担】
过量生产是指过程中,前制程制造的产品数量或时间超过了客户或后制程当期的最小需要量,白话表述为:生产的产品数量超过了需求,导致库存积压。
例如:某玩具制造企业在接到客户下季度 10 万件玩具订单后,由于担心生产能力不足或原材料供应问题,提前在本季度就生产了 15 万件。这不仅导致大量产品积压在仓库,占用了资金和库存空间,还增加了搬运和管理成本。过多的在制品还会使生产周期变长,先进先出的管理难度加大,产品积压时间过长还可能导致不良品风险上升。
并且,这种过度生产会掩盖生产过程中的一些问题,如设备故障、工序不平衡等,使企业失去了持续改善的机会。
过度加工 - Overprocessing:不必要的【修饰】
过度加工包含两层意思:一是多余的加工,即在产品生产过程中,进行了一些对产品最终功能和质量并无实际提升的加工步骤。二是过分精确的加工,当实际加工精度远超客户需求或产品本身所需的精度时,就会造成资源的浪费。
例如:在家具制造中,对于一些客户并不关注的内部零部件表面,进行了过度精细的打磨和抛光处理。
过度加工不仅耗费大量的人力和时间,还额外消耗材料和能源,或要求使用更精密的设备、更高级的技术工人,导致增加了生产成本,却没有给产品带来更多的价值。
缺陷(不良品) - Defects:质量的连锁损耗
缺陷(不良品)的浪费,是指生产过程中因质量问题导致的返工、报废等损失。当不良品产生时,企业需要投入额外的时间、人力和物力进行处理。在这个过程中,工人原本可以用于生产合格产品的时间被浪费在了修理不良品上,而且还可能需要额外的设备和工具来完成修理工作。同时,不良品若无法修复,就会变成废品,造成材料的直接损失。
若因不良品导致交货延迟,还可能引发客户不满,损害企业的信誉,带来潜在的订单损失。
未充分利用员工技能 - Skills:潜力未挖掘,人才埋没
未充分利用员工技能的浪费,是指未充分利用员工的知识、技能和创造力。
企业没有为员工提供足够的培训和发展机会,员工的技能无法得到及时更新和提升,不能适应不断变化的工作需求。长期下来,员工原有的一些技能也可能因为缺乏实践和应用而逐渐退化,造成技能浪费。
团队内部沟通协作存在问题,成员之间信息不共享,导致员工的某些技能无法被团队其他成员知晓和利用。
例如:在跨部门项目中,由于部门之间沟通障碍,某员工拥有的对项目有重要价值的技能未被发现和使用,从而导致技能闲置。
三
如何管控
摆脱浪费的紧箍咒
面对八大浪费的挑战,只要采取有效的措施,就能摆脱这些浪费的【紧箍咒】,实现降本增效的目标。
企业可以实施精益生产,通过引入精益生产理念,企业能够以客户需求为导向,优化生产流程,实现准时化生产,减少库存积压、生产过剩 。在这个过程中,企业可以运用看板管理、价值流分析等精益工具,对生产过程进行全面监控和分析,及时发现并解决问题,从而提高生产效率和质量。
优化生产流程也是关键。企业需要对现有的生产流程进行全面梳理,找出其中存在的不合理环节,如不必要的搬运、过度加工等,并进行优化和改进。通过合理布局生产设备,缩短物料运输距离,减少搬运次数;通过与客户沟通,明确产品需求,避免过度加工。同时,企业还可以引入先进的生产技术和设备,提高生产自动化水平,降低人工成本和错误率。
加强员工培训,提高员工的浪费意识和操作技能同样重要。企业可以组织员工参加相关培训课程,让他们了解八大浪费的概念、危害以及消除方法,培养他们的节约意识和成本意识。同时,企业还可以通过开展技能培训,提高员工的操作熟练程度,减少因操作不当而导致的浪费。
随着数字化的深入,科学技术的发展,价值流重构、数字化赋能、文化再造等等方案都能在摆脱【紧箍咒】上再进一步。
目前【八大浪费】被广泛接受,但并不意味着浪费的类型是固定不变的。随着生产技术的发展和管理理念的更新,新的浪费类型可能会被发现并纳入其中。
例如:随着数字化转型的推进,数据浪费(如数据冗余、数据不准确等)也逐渐成为生产制造中需要关注的问题。
此外,不同企业可以根据自身实际情况,对八大浪费进行进一步细化和扩展。
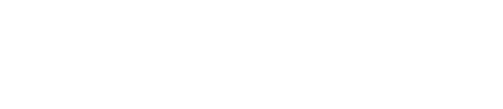
消除八大浪费并非一蹴而就的事情,需要企业全体员工的共同努力,从管理层到一线员工,每个人都要树立起消除浪费的意识,将其融入到日常工作的每一个环节中。同时,企业还需要建立起一套完善的持续改进机制,不断地发现问题、解决问题,持续优化生产流程,提高生产效率和质量。
制造企业的竞争,本质上是浪费消除能力的竞争。当每个员工都成为浪费的【猎人】,当每个流程都经得起显微镜式的审视,企业就能在成本岩层中凿出利润清泉。这场没有终点的改善之旅,正是中国制造向高质量发展的必经之路。
希望每一位企业管理者都能深刻认识到八大浪费的危害,积极行动起来,带领企业踏上消除浪费、降本增效的征程。